Can MJF Replace Urethane Casting?
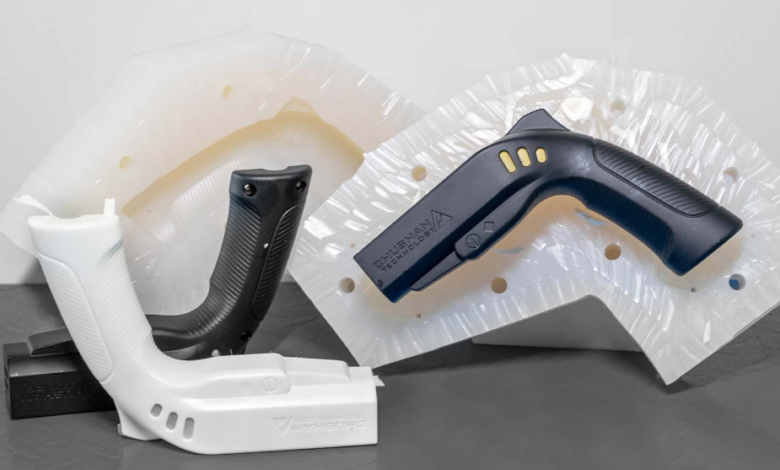
🔄 Rethinking Bridge Production
For decades, urethane casting has been the go-to solution for bridge production—used when volumes are too high for SLA prototypes but too low to justify injection molding. But with advances in Multi Jet Fusion (MJF), many teams are reevaluating that choice.
MJF offers similar benefits—fast lead times, high resolution, and low setup costs—with greater design flexibility, scalability, and mechanical consistency. However, urethane casting still has advantages in material variety and surface finish.
⚖️ MJF vs Urethane Casting: Process Overview
Urethane Casting
- Requires a master pattern (often SLA)
- Silicone molds used to cast parts in polyurethane resin
- Mold life typically limited to 15–25 parts
- Offers a wide range of resins: clear, rubber-like, high-temp, food-safe, and UL-rated
Multi Jet Fusion (MJF)
- Directly prints nylon parts from powder
- No molds or tooling required
- Uses PA11, PA12, and TPU for production-grade strength
- Limited in resin appearance options, but excels in geometric complexity and durability
See also: AI Face Swap Technology and Its Role in Virtual Reality
💰 Cost and Lead Time Comparison
Factor | MJF | Urethane Casting |
Tooling Cost | None | Moderate (pattern + mold) |
Per-Part Cost | Low at volume | Low for very small batches |
Lead Time | 2–5 business days | 1–2 weeks (mold required) |
Design Flexibility | Very high (no mold constraints) | Moderate (requires draft angles) |
Scalability | Excellent (scales to 10k+) | Limited (mold wear, low volume) |
Material Options | Durable nylons + TPU | Broad (clear, soft, UL, food-safe) |
🧠 When MJF Wins
- No tooling delay: You print directly from CAD
- Design freedom: Complex geometry, undercuts, and internal channels with no draft angle
- Stronger parts: Engineering-grade thermoplastics with isotropic mechanical properties
- Better scalability: 1 to 10,000 parts without mold wear or repeat setup
MJF is ideal for short-run production where strength, speed, and repeatability matter more than ultra-specific material properties.
🧪 When Urethane Casting Wins
Despite its limitations in scale, urethane casting still holds key advantages:
- Clear materials: Ideal for lenses, housings, or aesthetic models
- Flexible durometers: Shore A and Shore D resins for soft-touch parts
- Specialty performance: UL-rated, FDA-compliant, food-safe, or high-temp formulations
- Glossy finish: Molded parts replicate the finish of the master pattern without post-processing
Urethane casting is a better fit for:
- Marketing models
- Functional elastomers in very specific hardness ranges
- Compliance-heavy industries needing certified resins
🎨 Surface Finish and Appearance
Feature | MJF | Urethane Casting |
Default Finish | Matte, lightly textured | Glossy or polished (mold-dependent) |
Post-Processing | Dye, tumble, vapor smoothing | Painted, tinted, or cast-in color |
Visual Prototypes | Good | Excellent |
Functional Surfaces | Strong and consistent | Smooth but variable |
🏁 When to Switch from Urethane to MJF
Choose MJF over casting when:
- You need more than 25–50 parts
- You’re iterating quickly or designs aren’t locked
- Your geometry is too complex for silicone molds
- You want to scale into repeatable, production-grade nylon
Choose urethane casting when:
- You need clear parts or soft-touch elastomers
- Your project requires certified materials (e.g., food-safe, UL-rated)
- Surface gloss or true color matching is critical
Print or Cast? We’ll Help You Decide
At RapidMade, we work with clients every day to evaluate whether to print or cast. In many cases, MJF outperforms urethane casting for function, speed, and cost—especially once volumes grow or the design stabilizes.
Want to compare both options? Upload your file at rapidmade.com and we’ll run a side-by-side quote.